It may seem incredible that small things such as labels can make a significant difference for large, advanced machines in the production environment. And in themselves, labels are not large components, but a well-functioning label is important for documentation and maintenance of the machines. If the labeling ensures the necessary flexibility and easy identification, then the labeling also has a certain significance.
TRESU Group has benefited from a labeling solution provided by Hans Følsgaard A/S. TRESU Group employs 260 people globally and is headquartered in Bjert, south of Kolding. The company manufactures printing machines, predominantly used in export markets for packaging printing. Most solutions are made in close cooperation with the customer and range from mobile units to lines around 80 meters in length.
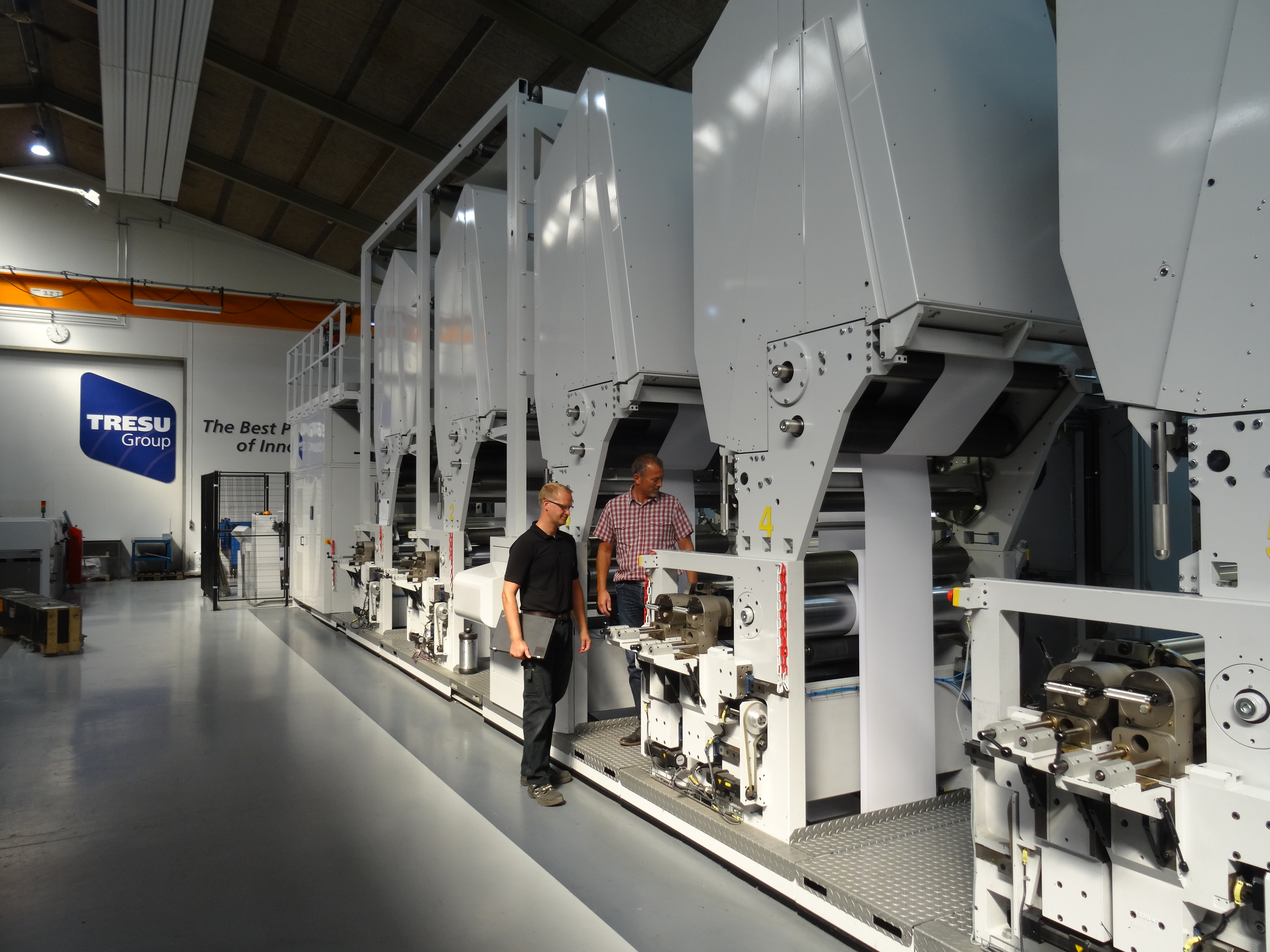
Tresu A/S printing machines range from mobile units to about 80-meter-long lines as big as houses. The machines are all specialized products that use a number of tubes for pneumatics and the conveyance of fluids. Identification is therefore important.
The company has production facilities in Denmark and the USA, as well as sales companies in Germany, Italy, Japan, and China. Some components are purchased as standard products or manufactured by subcontractors, but development, design, and assembly take place in Bjert. Among the purchased products are several components from Festo, which are connected to the controls via tubes that control the pneumatics in TRESU's advanced machines.
- The final assembly of the machines we manufacture at TRESU Group requires a connection of a larger network of both pneumatic and lubrication tubes. We typically use tubes in dimensions that increase in 2mm steps from 4mm to 16mm in diameter. The tubes must, of course, be clearly labeled, both for correct assembly and documentation, and with regards to service intervals, explains supervisor at TRESU Group, Martin Bøgedal Rasmussen.
Previously, tube labeling had been a challenge for TRESU's installers, and Martin Bøgedal Rasmussen had therefore been looking for a labeling solution that could provide a higher degree of flexibility and functionality than the somewhat rigid wrap-around labels. There's nothing wrong with the wrap-around solutions, as they provide the necessary labeling. But once such a label is in place, it's difficult to adjust the label slightly if a tube needs to be shortened, and it's also impossible to rotate the tube so the label is visible from the inspection side of the machine.
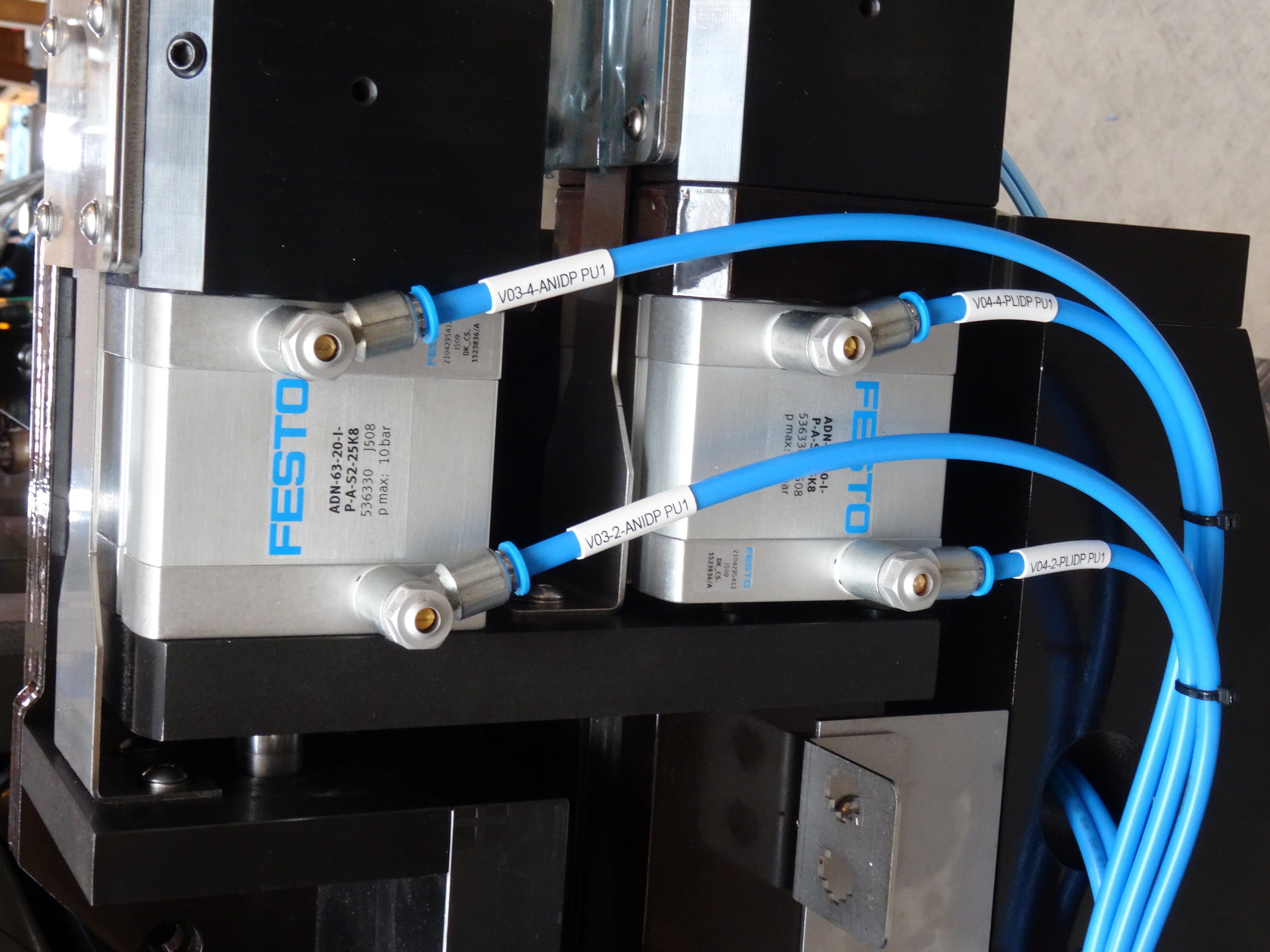
The labeling tubes are pulled over the tubes that need identifying. The solution that Link Solutions via Hans Følsgaard A/S has come up with allows for the label to be rotated or adjusted. But the label cannot move itself without physical impact. This provides a flexible as well as assembly and service-friendly solution.
Close Danish Development Cooperation
According to Martin Bøgedal Rasmussen, the ideal solution for labeling the tubes in the machines would be a soft, halogen-free outer tube that could be printed with the current labeling. The labeling tube should have a slightly larger diameter than the pneumatic or lubrication tube it was marking. With such a solution, it would be possible to move the label up and down the tube and rotate the label, so readability would always be optimal. However, the diameter must not be so large that the label could move by itself.
Hans Følsgaard A/S represents the Odense-based company, Link Solutions, in Denmark and Norway. It is a company founded and run by dedicated labeling professionals, and Link Solutions has the technology TRESU Group needed – albeit not quite in the right sizes. TRESU Group had previously received products from Link Solutions through another distributor, part of a larger international chain of dealers, but this company only operated with a standard program.
- It was considerably easier to talk with Hans Følsgaard A/S, who quickly got Link Solutions involved in the task. And Hans Følsgaard was good at solving the teething problems that almost necessarily arise when a new technology needs to be implemented. Even though it sounds reasonably simple to pull a labeling tube over a pressure tube, there were some initial challenges. But here too, it's beneficial to have a medium-sized, local distributor who takes responsibility for the task, observes Martin Bøgedal Rasmussen.
The collaboration between Link Solutions, Hans Følsgaard, and TRESU Group is a fine example of a Danish model, where communication between customer, supplier, and developer is as swift as possible. This has made it possible to ensure that a given program from a supplier can be adapted for specific purposes, ending up with a solution that is not just good, but which gives an end customer like TRESU Group a technical competitive advantage.
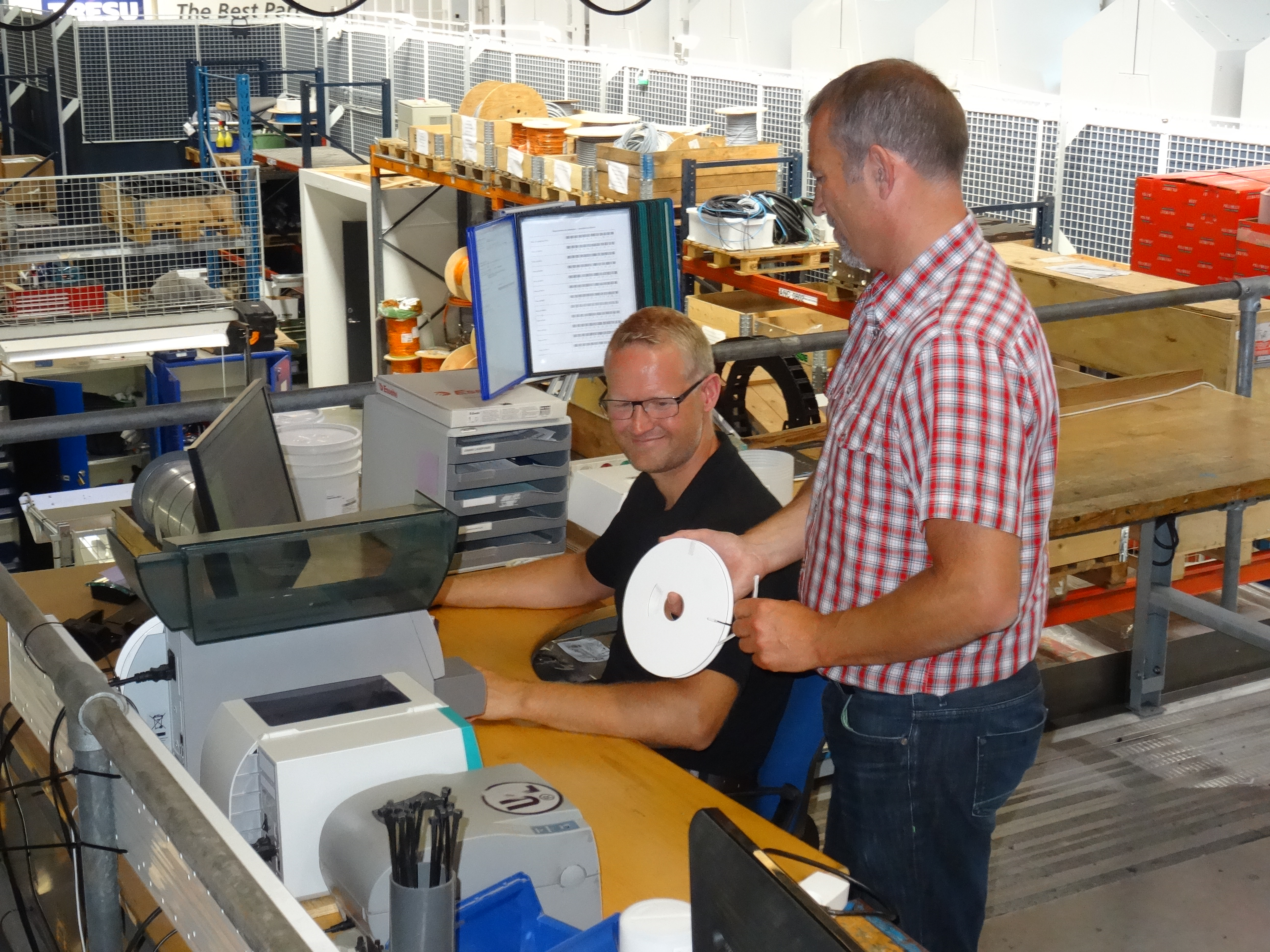
Article author, Teddy Tofte Hansen (front), from Hans Følsgaard A/S together with TRESU Group, supervisor, Martin Bøgedal Rasmussen, who initiated the creative solution
The Technical Specifications are Fully Met
But of course, there have been bumps along the way. Had the solution been straightforward, there would probably have been several takes on a model that TRESU Group could have used. The labeling tubes are delivered in spools, which are run through a printer for labeling. This has the advantage that all labels for a given machine can be printed as one task. The labeling tubes come out in one go, along the way being perforated, so the assembly can actually be performed without the use of tools. But when the label has to be pulled down over the tube to be labeled, a circular shape is, of course, a requirement. It took some work to optimize this aspect.
TRESU's supervisor, Martin Bøgedal Rasmussen, emphasizes that it is not necessary to use heat for the assembly of the labeling tubes. Cable ties can also be avoided, which allows for a very rational production. Most importantly, however, is that the labels can be adjusted or rotated as necessary, not only easing assembly but also subsequent service and maintenance in the field, where it's possible to shorten the tubes without having to re-label them.
Link Solutions has, of course, tested materials and print according to the specifications and the chemistry TRESU Group uses. Among the current tests are swipes with the chemical substances the labeling typically comes into contact with. It should, among other things, be possible to swipe the labels ten times without loss of readability. It also eases tasks that the total labeling for a machine can be printed as one job, which is then perforated and cut. The labels for the individual machines can thus be included in Tresu A/S' logistics as one construction or spare part.
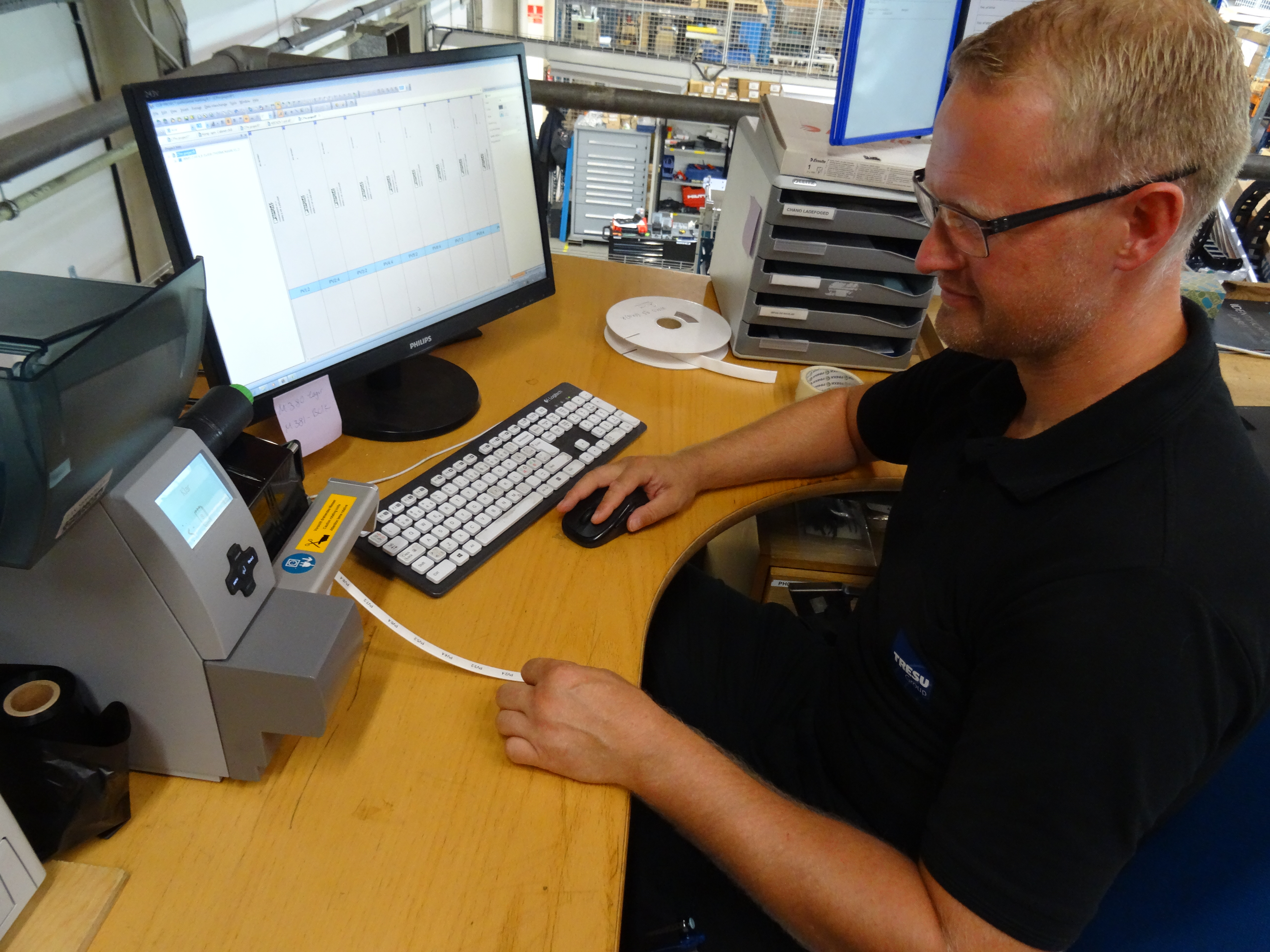
Martin Bøgedal Rasmussen tager et mærkningsjob ud af printeren. Mærkningsslangerne er nu perforerede og printet i en ubrudt længde svarende til et aktuelt maskinjob.